|
|
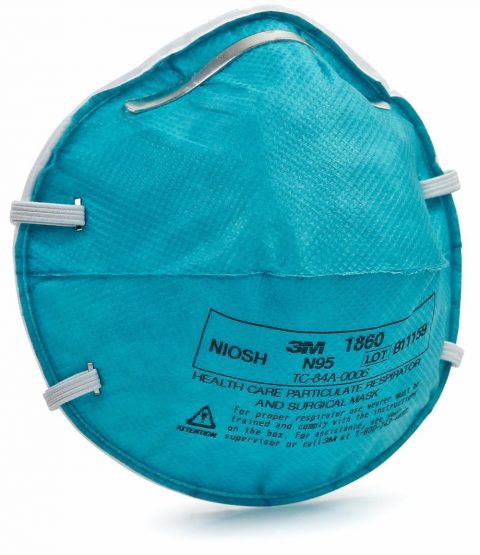
As companies of all kinds are changing their manufacturing operations to make PPE during the COVID-19 pandemic, preexisting PPE manufacturers are trying to rapidly expand their capacity and output. A recent article in Bloomberg highlighted how 3M, a manufacturer of the N95 respirator, is able to do this.
[3M, the maker] of Post-its, Scotch tape, touchscreen displays, and scores of other products—has been preparing for almost two decades. Coming out of the SARS epidemic of 2002-03, the company realized it wasn’t fully equipped to handle unexpected explosions of demand in the event of a crisis, or what it calls an “X factor.” It decided to build surge capacity into its respirator factories around the world.
There is a relatively steady need of N95 respirators for healthcare, construction workers, and everyday consumers (I once sanded a derelict sailboat while wearing one of these), but additional demand for respirators spikes depending on the type and scale of the incidents that necessitate their use.
“We realized we didn’t have the ability to flex” production to adapt to the unexpected. “We had H1N1 after that, we’ve had forest fires and hurricanes, and all of those create a surge in demand.” So 3M set about rethinking the manufacturing process from one end of the supply chain to the other. Factories added assembly lines that would stand dormant until needed. Suppliers were put on alert. The company assembled emergency response teams that would leap into action whenever catastrophe beckoned: Harvey, Maria, the California wildfires.
An important factor in surge capabilities is logistics. Even if you have the capacity to increase production, if you’re relying on a global supply chain and that falls apart, you’ll be missing key components and materials needed for manufacturing.
3M had another built-in advantage: Unlike many companies that have moved production to low-cost countries, it sources the materials for its respirators near its assembly plants and serves customers reasonably close by. “We make respirators in China for the China market, we make respirators in Korea for a little more than the Korea market,” Roman says. Each plant can ship respirators anywhere—pretty important in a pandemic—but day to day, a plant doesn’t rely on distant vendors subject to tariffs or export bans.
Even if no countries allow the export of the N95 respirator, 3M will still be able to supply people around the world (if not everybody, at least multiple countries and populations). The politics of pandemics can get complicated, and as bad as COVID-19 is, things could be a lot worse. The way 3M is set up now, they aren’t bound to a single state.
PPE is a unique industry to be in, but there are generalizable lessons to be learned here as it relates to manufacturing, international logistics, and contingency planning. Read the whole article over at Bloomberg for more.
|
|
|
| |