Manufacturing a new product requires development, feedback, troubleshooting and iteration. Many manufacturers can forget that first builds are often rough drafts, and ironing out the kinks before the switch to full scale automation or massive production is part of the manufacturing process.
Over on Medium, Ruth Grace Wong tells the story of Kevin Liang, who managed the first build of a Kickstarted aquarium and learned this lesson the hard way.
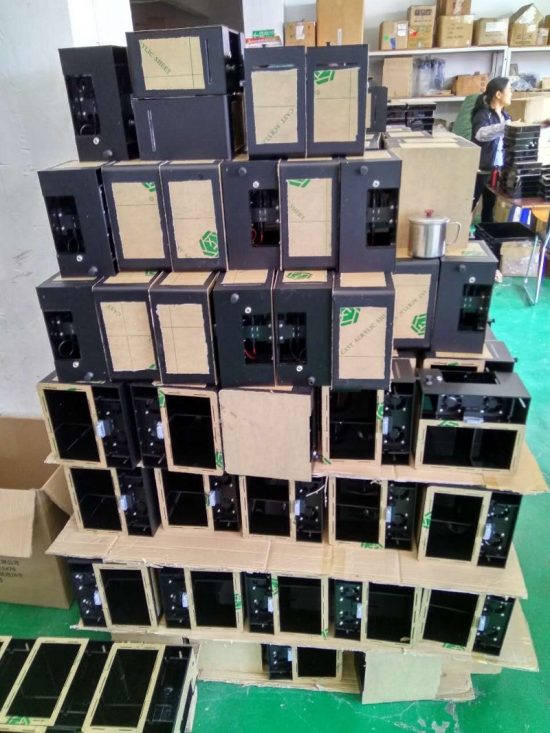
When the first production sample was delivered, it had multiple problems: The filter was leaking, there were bubbles in the clear plastic right up front where the LEDs were, and the clear part of the filter lid where you could see the water flowing through was bent and didn’t fit.
For first production samples, this can be expected.
“This is just a part of the process,” Kevin [later explained]. “If I didn’t speak Chinese, I could have easily made up my mind and said [the issues] were because they’re Chinese and this is the type of work they do. As Americans the gut reaction can be ‘What do you mean it’s leaking? You should be fixing it!’ but the factory is just involving you in the development. The first sample is the rough draft.”
The first few builds always have this potential, manufacturing a new product has unforeseen surprises. Working flexibility into the processes is essential — a good goal is to use the first build to inform later, larger builds. Setting up some “guardrails” is a helpful practice.
Jasmine hired Xiagong, a plastic engineer, on commission to help them figure out what machines they needed to buy and how to set up production and train the workers.
It turns out that sheet acrylic manufacturing, while cheaper than injection mold tooling at low volumes, comes with its own challenges. The workers have to be trained to glue the parts. Kevin made it clear to the factory that bubbles in the acrylic glue seams were unacceptable, and the factory wasted a lot of plastic while training the workers because of bubbles. “Jasmine is putting in more work and more time, and they had to waste a lot of product to figure it out, but her margins are significantly higher than another factory… Manufacturing moves from country to country, but what stays is high end, high margin goods. Not a me-too product. This is because of the technical skills required.”
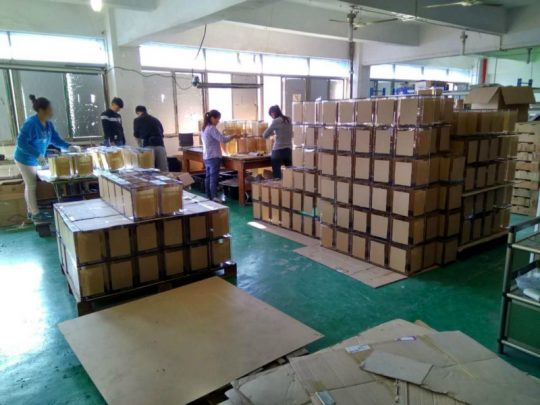
This is good manufacturing: attention to the build, noticing problems, ironing them out, and incorporating them into the next. Liang notes that paying for this is worth it.
The whole story is quite a saga and has some good lessons. Read it all here.